Tank Mix Sequence Guidelines
Correct Mixing Order and Procedures Increase Productivity, Reduce risk
Compatibility problems can cost applicators a lot of time and money — in wasted product, spraying time due to plugged sprayers and even lost customers — when the job isn’t done correctly.
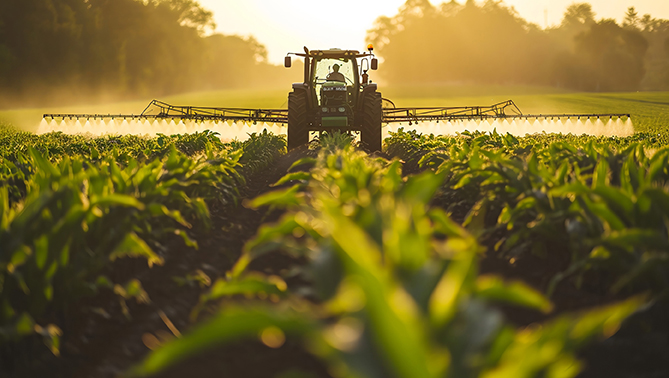
General Recommendations
It is recommended that a compatibility test be done prior to mixing any combination of crop protection products. If using a mixing vat or inductor, make sure there is adequate agitation and a minimum of 15% of the desired finished spray volume carrier in the mixing vessel prior to diluting the crop protection products. If the mixing vessel cannot hold the required minimum volume, open the valve and add the crop protection products in the recommended order.
Mixing Sequence
1. Sulfonylurea Herbicides
- *Add before reducing pH, or pre-slurry in 5 gallons of water at pH 8.5-9.5, and add once completely dissolved.
- Use 2-4 oz of household ammonia in 5 gallons of water to raise pH to desired level.
2. Compatibility Agents and Defoamers (Convert™/Gundown Elite™, Knockdown™)
- *Compatibility agents will reduce spray solution pH.
3. Dry Products
- Ammonium sulfate and dry micronutrients
- Drift retardants
- WP, DF, WDG, SP formulations
4. Liquids
- Drift retardants (Direct™ RS, Border Xtra 8L, Intact™, Intact Advanced, Taragon™ Elite, TaragonXtra, or Transport Plus™)
- Suspo Emulsions (SE)
- Aqueous Suspensions (AS)
- Flowables (F or FL)
- Micro encapsulated (ME)
- Suspension concentrates (SC)
- Liquid Concentrates (LC)
- Emulsifiable concentrates (EC)
- Solutions (S or SL), liquid and concentrate suspension fertilizers, chelated micronutrients and growth hormones
- Capsule Suspensions (CS)
- Adjuvants
- Crop oil concentrates (Vigor™)
- High surfactant oil concentrates (Exchange™, Volare DC™ or Kixyt ™)
- Methylated seed oils (MSO Ultra™ or Persist® Ultra)
- Oil-based DRT (Nexum™)
- Nonionic surfactants (Vertex™, NIS 80:20™, NIS 90:10™, Speed™ or Chem-Stik™)
- Water conditioning agents (Deriva™)
Improper Mixing Sequence
Even a slight change in mixing order makes a huge difference in product efficacy and compatibility. Something as simple as reversing the mixing order between a flowable (F) herbicide, like atrazine, and an emulsifiable concentrate (EC), like 2,4-D, can cause a cottage cheese-type consistency that will plug sprayers. Other mixing errors increase the amount of residue and buildup on the interior sidewalls of the sprayer’s tank leading to longer cleanout times and the increased risk of cross contamination.
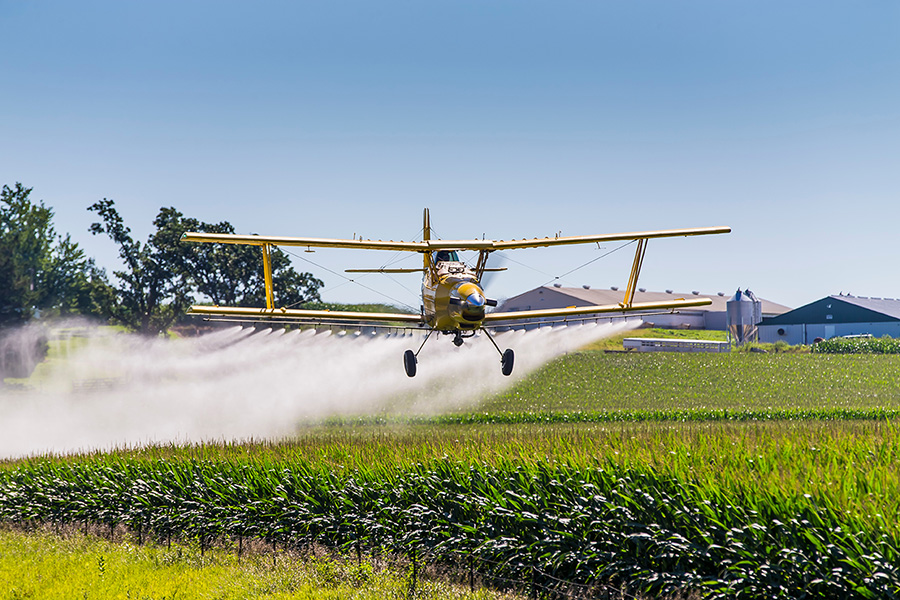
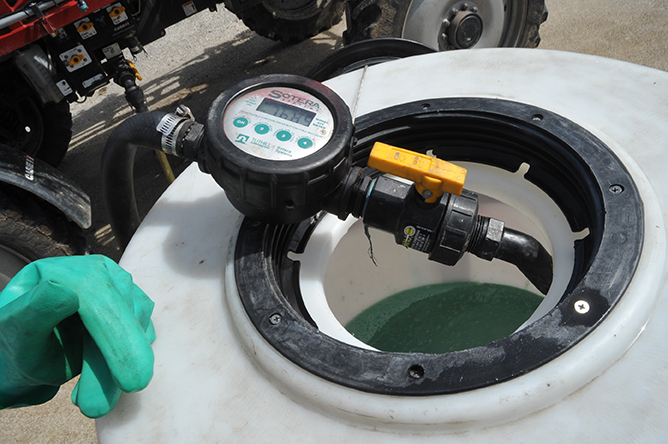
Fixing the Mixing Sequence
Make sure that you add products in the correct order. Most crop protection product labels state a preferred mixing sequence. If you’re still not sure, simply conduct a small compatibility test to verify the mixing order that produces the most stable tank mix. Directions for conducting compatibility tests can be found on crop protection labels. If you want to learn more about proper mixing order, watch the compatibility video on our YouTube channel.
The Root of the Problem
Before glyphosate-resistant weeds began to emerge it was not uncommon for applicators to mix water-soluble liquids like glyphosate and surfactant together in an inductor or mixing vat with little or no water, and with little or no problems. But times are changing. More glyphosate resistant weeds means more tank mixing with tank-mix partners that aren’t water-soluble, leading to compatibility problems.
The two leading causes of incompatibility problems are:
- Little or no water to dilute crop protection products when using a mixing vat or inductor cone.
- Improper mixing sequence.
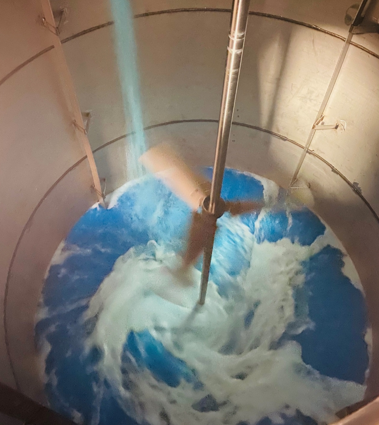
Mixing Vats and Inductor Cones
Are you creating a new crop protection formulation? When combining undiluted crop protection products and adjuvants in a mixing vat or inductor cone that’s what you’re doing. These new “combinations” were not formulated to be together, undiluted, so they often begin to gel or salt out quickly. The good news is they usually rinse out of the mixing vat or inductor cone easily. The bad news is you’ve now transferred the problem to your sprayer, leading to plugged screens, lines and nozzles.
The Mixing Vat Solution
If you’re going to use a mixing vat or inductor you have two options to avoid tank mixing problems:
- Add enough water to the mixing vat or inductor cone to dilute your tank mix partners. This is usually no less than 10-15% of the entire volume of the anticipated spray load. Example: 1,000 gallon load requires an inductor cone or mixing vat that can hold 100-150 gallons of water.
- If your mixing vat will not hold the appropriate levels of water, then you should open the valve and add products individually in the proper mixing order. Follow each product with a water rinse before adding the next
How Compatibility Agents Work?
Stable tank mixes form milky emulsions, like those in the container on the left in the adjacent photo. The middle container in the adjacent photo shows what can happen when liquid nitrogen is mixed with an herbicide without the use of a compatibility aid. The container on the right had the same mix with liquid nitrogen and the compatibility aid, and shows just how little residue is left behind when products are properly suspended.
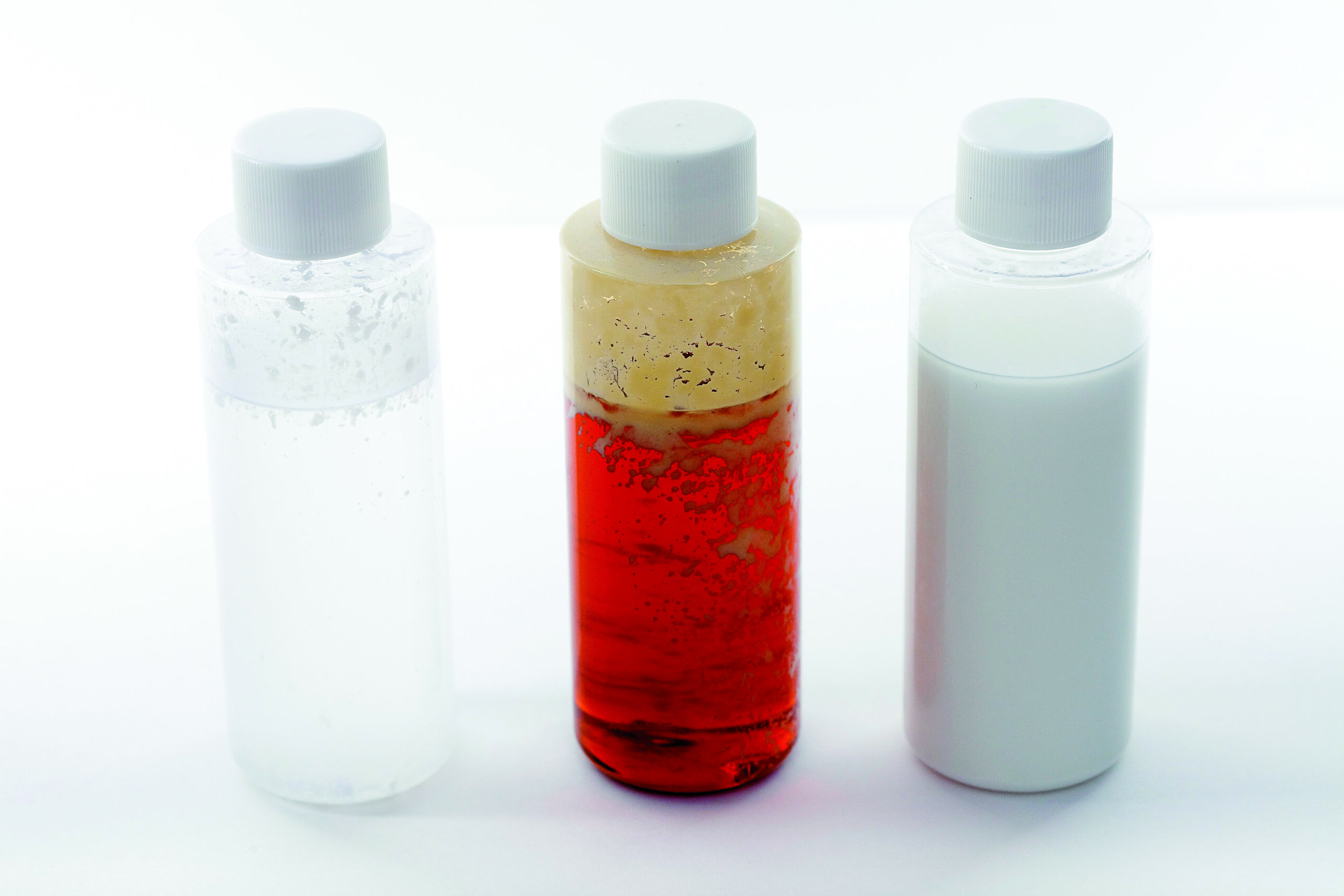

How can we help?
Can't find what you're looking for or need additional information? Let us know how we may assist you and we'll respond as soon as possible.